In an era where speed, sustainability, and cost-efficiency are considered paramount, modular construction is emerging as a viable way for companies to deliver projects on time, and on budget. With modular components manufactured off-site and assembled with precision, this cutting-edge approach is revolutionizing the way buildings are conceived, designed, and erected. At the forefront of the modular construction boom in Ontario is Central Precast, previously featured in the May ‘22 edition of Apeiron Construction.
It’s a testament to the advantages of modular construction that since we last spoke, Central Precast has already successfully delivered several modular projects that were in the pipeline back in 2022. As modular construction enjoys something of a boom in the industry, Stefano Mion—Estimator at Central Precast—believes the advantages for businesses are clear. “I think people can realize the benefits of modular construction such as efficiencies on site, reduction in subcontractors or trades on site that they need to manage. We’re able to erect entire structures in one to five days where a conventional build can take weeks or months.”
It’s not just build-time that’s dramatically reduced, adopting a modular approach also greatly streamlines the construction process. “In conventional builds, our clients are organizing multiple trades, contractors, daily supplies etc. Whereas with modular construction, they’re really only dealing with us. You’re going from managing half a dozen trades down to just one.” Then there are other efficiencies from manufacturing off-site. “There’s definitely less waste with modular because we’re only forming and supplying what’s needed for the building. When a building is erected on site there’s significantly more material waste.”
As part of the third generation of the Mion family to work at Central Precast, Stefano follows in the storied footsteps of his father, John, and grandfather, Luigi, who started the company 67 years ago after emigrating from Italy in the 1950s. Having made their name as one of the largest and most diversified precasters in Ontario, Stefano and his family are already well-versed in fabricating building materials off-site. “My grandfather started out manufacturing small, simple items, such as steps and slabs; small items that could be fabricated in his garage. Essentially, he was looking for efficiencies in the construction industry and trying to fill a void in the market.”
Though the company is now enjoying a period of continued growth, in the early days there was some skepticism around precast materials, “Precast was still a bit of a new concept, even to this day, there’s still sometimes a little reluctance to using it. But we always knew that if we kept delivering viable products in a timely manner then it would become accepted by the industry and used more and more.”
It wasn’t long before clients and contractors started to realize the benefits of precast. “They started requesting different items for their projects and my grandfather kept making more and more and different products.” It’s an approach that’s served Central Precast well over the years as the company’s product offering has expanded rapidly. “We’re well known and we’re one of the largest retailers for concrete products and we’re always looking for trends to diversify our product line. We eventually got into infrastructure products like pipes and manholes, and then utility products like transformer bases and spun concrete poles. Whenever clients made requests for different products, if we were able to make it, we would try to offer it as a product line.” One such example is Central Precast’s recent expansion into natural stone. “We spotted a trend towards using natural stone, so we just felt it was a good opportunity to expand it to the market.”
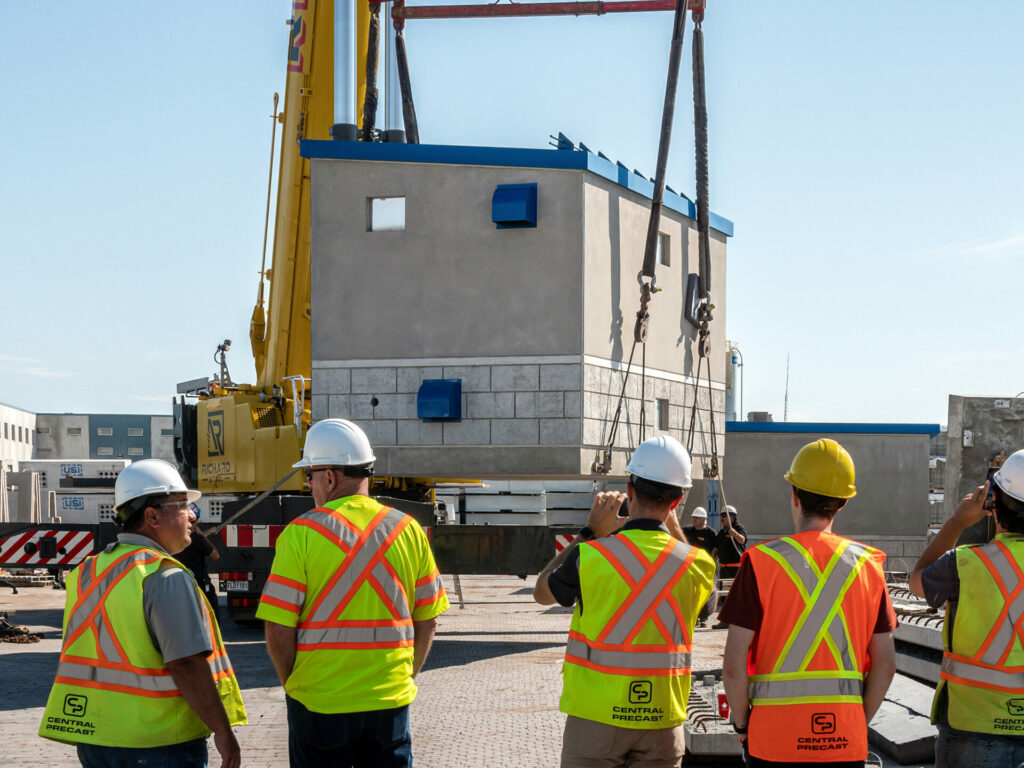
These days, the Central Precast brand is fast becoming associated with projects in the modular construction space, including shipping its largest modular building to date in Geraldton, Ontario. As Stefano explains, however, larger projects can come with their own challenges. “The bigger the building, the more risks are involved. So now you’re dealing with overheight permits and there are restrictions on when the building can be transported throughout the day. On top of that, there was construction along the route, so that that minimized the time that the building was actually allowed to be shipped along that route because of its size.” In spite of the challenges, Central Precast was able to deliver the project successfully, further solidifying its stellar reputation in the industry.
Another recent project that showcased the versatility of both modular construction and Central Precast’s approach was the Wateridge Village housing development in Ottawa. Tasked with creating a hydro vault on the development, Stefano and his team were asked to create something that harmonized with the existing structures. “We try to be flexible and to accommodate customer requests as much as possible. Their concern was that they didn’t want just plain concrete as a final finish of the product. So, this was a good opportunity to use different finishes and multicolor staining techniques to match the adjacent buildings in that development.” As he goes on to explain, collaboration was key to achieving the desired results. “They brought us physical samples for the brick and siding so we could match the finish to those adjacent houses.” With insulated precast wall panels, simulated brick patterns, and a color palette matching the surroundings, the hydro vault fits seamlessly into the built environment, showcasing Central Precast’s knack for innovation, aesthetics, fire safety, and most importantly, delivering the project on time.
“With insulated precast wall panels, simulated brick patterns, and a color palette matching the surroundings, the hydro vault fits seamlessly into the built environment.”
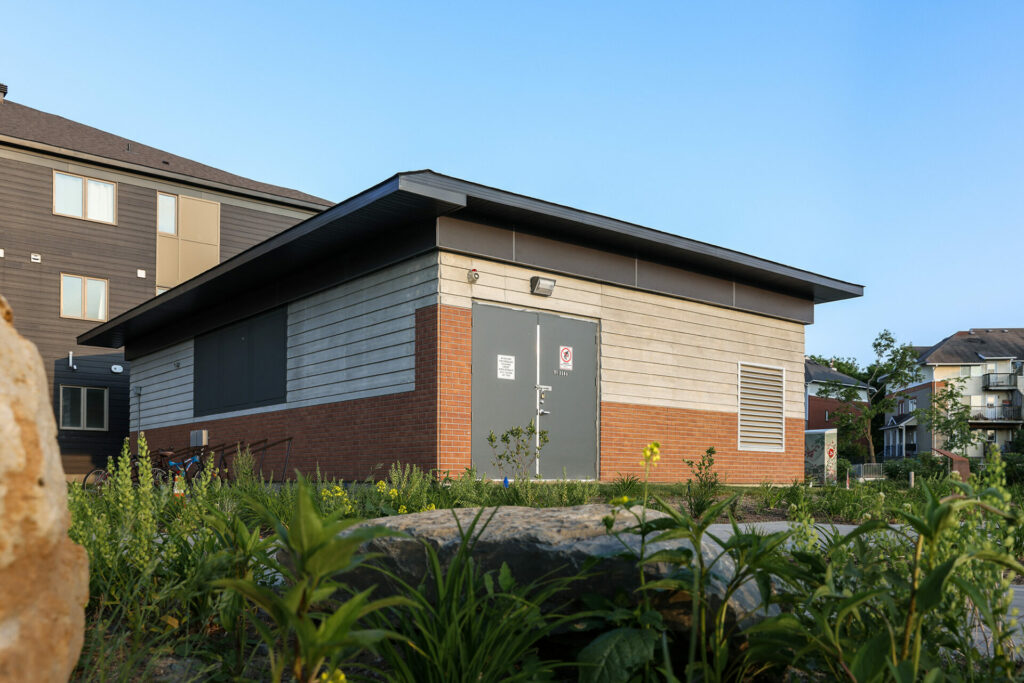
It’s this unwavering attention to detail that’s allowed Central Precast to develop such a strong reputation in the industry, something that Stefano highlights as a key reason for the company’s continued success and longevity. “I think it’s just about being reliable and having that reputation for continuously trying to provide good quality products and customer service for the industry.”
Looking at the current challenges facing the industry, labor shortages are frequently cited as one of the key concerns for leaders in construction, but Mion sees this challenge from a different angle. “For us, there’s a larger focus on retainment. Retaining current staff could be as important, if not more important, than recruitment.” It’s not an entirely surprising answer from a company with such strong family bonds, after all, Stefano works alongside his brothers Marco and Carlo L., and cousins Claudio, Carlo E., and John Licari. The family feel is something the company has been keen to maintain. “We run several training and skills programs that we offer to our employees, but we’ve also done a lot of initiatives just to benefit the people that work here, whether that’s company barbecues and food trucks, the branded gear we hand out, even down to the annual Christmas party.”
As the team at Central Precast looks ahead, Stefano sees modular construction as a potential way it can meet the growing needs of the industry. “There’s demand for faster offsite, modular construction. So, with increasing labor shortages, total precast systems can help solve these problems. I think this could well be the future of the industry and it’s definitely an area that we’re going to put a larger focus on in the coming years.”
Photos by Carlo L. Mion / Central Precast