Around the world, societies and industries are attempting to devise solutions to the great problem of our time, sustainability. By coupling a global economy with a single-use mindset, we have contributed to a situation that now requires urgent action. Simply put, our planet is in serious danger and it seems as though a complete shift in mindset is required to reverse, or at least slow, the most severe effects of climate change. No industry can claim to be perfect in this regard and construction is certainly not without its faults. Where the industry does differ, however, is that innovation and an opportunity to improve things can be found in the companies and inventors and producers throughout the construction world. While we can always be better; solutions do indeed exist.
While carbon emissions are regarded as the main offender in terms of environmental damage, there are other, more tangible issues that need to be tackled also. Plastic, while a helpful and versatile product, is the cause of great difficulties the world over. It is one of the most widely used materials in the world though historically there have not been circular end-of-life solutions available. The facts around plastic, its uses and its post-use effects, are staggering and make for grim reading. The sobering reality is that around 91% of all plastics are not recycled and end up either in landfills or in waterways. Additionally, by 2050 there will be more plastic in the sea than fish. The net result of this is “post-use plastics end up choking waterways, harming vulnerable ecosystems, and often can even end up in our bodies in the form of microplastics.” This is not scaremongering; it is fact, and our industry is required now more than ever to make environmental impact changes. In fact, with a track record of innovation and ground-breaking advances, the onus is on construction companies to use its skills to develop new techniques to combat these potentially devastating issues if it can.
Five years ago, a group of engineers set up a company to do something about this and over this time, Brightmark has recycled over four million pounds of plastic. From the beginning, the goal has remained a simple one; “We created waste solutions that not only contribute to lowering greenhouse emissions but also keep plastics in use and out of landfills, waterways and incinerators.” However, this company is now going even further. With a mission to “discover and provide circular solutions to some of the world’s most pressing waste challenges, including turning organic waste into clean, renewable energy and closing the loop on the plastic waste crisis through innovative circular solutions,” this is a company that is thinking outside the box.
So, what are “circular solutions” and how will they positively impact the environment? According to Brightmark, it is a sustainable model that, if adopted in a widespread fashion, could have huge positive effects on sustainable practices. “It is a system designed to keep waste out of a production’s manufacturing and consumption phases. Wherever possible, raw materials are preserved and reused, or recycled into new products. The circular economy aims to keep products, equipment, and infrastructure in use for longer, thus improving the productivity of our resources. We continue developing this technology to become an integral part of the circular economy.” This can only be achieved by shifting the mindset of consumers globally. “Beyond the current single-use waste economy, a circular economy aims to redefine growth, focusing on positive holistic benefits. It entails decoupling economic activity from consuming finite resources and designing waste out of the system.”
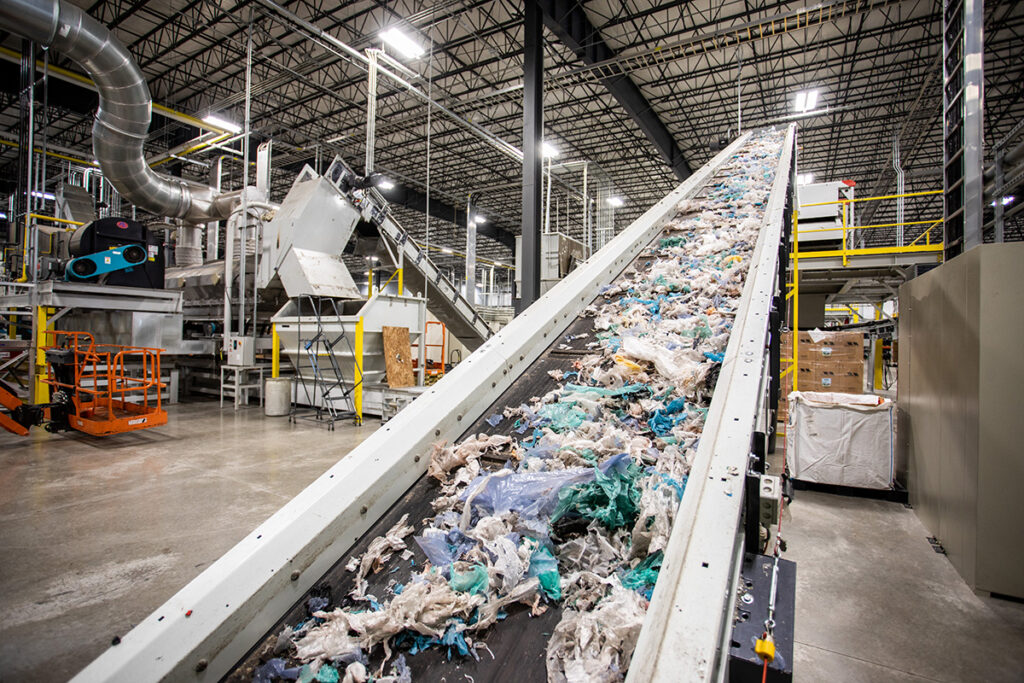
It must be acknowledged that this does indeed sound like a good idea, in theory. However, in order to reboot a culture that is accustomed to disposable products, the alternative needs to stand up on every level, from flexibility to quality. Thankfully, Brightmark have this covered. As the world’s first, and only, recycler of Grades 1-7 plastic at this scale, the company can take all plastic types and uses them to make genuine changes across countless industries. “We recycle all plastic types 1-7, unlock their value, and create new products. We are the only company that can take all plastic types 1-7 and then provide real solutions at this scale. We’ve built the largest advanced plastics recycling facility in Ashley, Indiana—and we’re just getting started.” The process itself is equally impressive. The plastic is shredded, dried, and turned into pellets. These pellets, incredibly, have a dual use. In addition to being reused as new plastics or wax, it also works as a source of fuel. When heated, it gives off a hydrocarbon liquid that can be used across multiple industries in hugely innovative ways. “By heating our pellets in a vaporized, oxygen-starved environment we can create a lower-carbon, commercial-grade ultra-low sulfur diesel to power the vehicles of today.”
“As the world’s first, and only, recycler of Grades 1-7 plastic at this scale, the company can take all plastic types and uses them to make genuine changes across countless industries.”
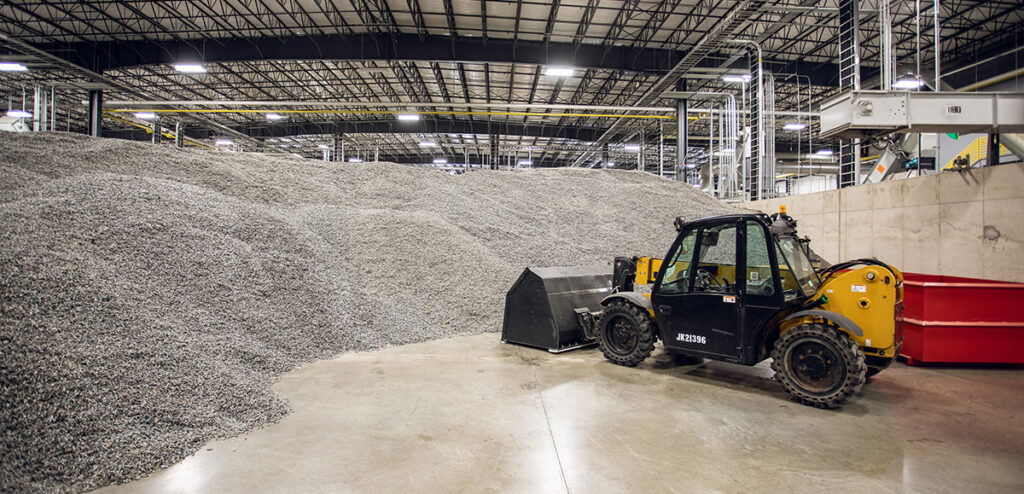
To date, the company has recycled four million pounds of plastic waste. It is not hyperbolic to suggest that, by the looks of things it is only getting started. Each Brightmark Plastics Renewal Facility processes a minimum of 100,000 tons per year of mixed waste plastic and turns it into valuable products and its goal is to offset 22 million metric tons of CO2 by 2025 and divert 8.4 million metric tons of plastic from landfills. While the company accepts that challenges remain, it is taking a long-term view. With a dual stream strategy that reuses and repurposes the plastic, the company anticipates further growth in the area. “It has been confirmed that 82% of the products produced can be used for circular applications, and we’re working on additional circular technology solutions and our plants are our centers for research and development. Currently, we produce naphtha, ultra-low sulfur diesel, and wax from the crude oil and natural gas that has already been extracted and processed during the production of our plastic feedstock. Research shows that developing fuel from advanced recycling processes like ours leads to a 39%-139% reduction in carbon emissions versus extracting new petrochemicals from the ground. We anticipate that every one of our future facilities in the United States and worldwide will be focused on a plastic-to-plastic manufacturing model.”
It is not often that a process comes along that can offer a genuine reason for hope. This exciting piece of innovation is truly at the cutting edge of sustainable technology and, tantalizingly, huge success is being seen in a short period of time. Ongoing challenges face us all, not only the construction industry. For too long we have allowed consumerism to run wild, filling landfills and pumping carbon into the atmosphere. Those at Brightmark are bringing something new to the table; an opportunity to rewrite the rulebook when it comes to plastics.