To do business in a way that is efficient, durable, and lucrative, is to respond to market trends and offer solutions to socioeconomic and industry challenges. That is, to provide a service that is useful to the market in which you operate. In Ontario, a growing market trend is to build up instead of out. One of the socioeconomic challenges is a lack of affordable housing and an increased demand for rental properties. And a major industry challenge is the post-pandemic labor shortage which continues to have a critical impact on construction practices. The answer? A company like Magest Building Systems Ltd, who specializes in delivering multi-story buildings using a system that is less labor intensive than traditional methods. Today, Magest specializes in the design, manufacturing, and assembly of cold formed steel (CFS) stud wall panels, floor joists and trusses as a complete panelized building system for framing multi-story buildings. It’s portfolio spans across Ontario and beyond, and includes Condominiums, Apartment Buildings, Hotels, Retirement Homes, and Student Residences.
Magest Group Limited was founded in 1990 as a general contracting company, which specialized in the supply and erection of pre-engineered steel building structures. “Our pre-engineered steel buildings contained a large quantity of cold-formed steel girts and purlins required to frame out the walls & roof,” says Craig Wood, Business Development Manager. “After erecting pre-engineered buildings for quite a few years, we decided to get into the cold form steel market in 2005. That’s when we decided to look into the design, supply and erection of load bearing steel stud wall panels, which would primarily compete with masonry block, poured concrete, and slower, more conventional construction materials. Supply and installing load bearing steel stud wall panels is very fast and efficient compared to conventional methods of construction which are very slow and more labor intensive.”
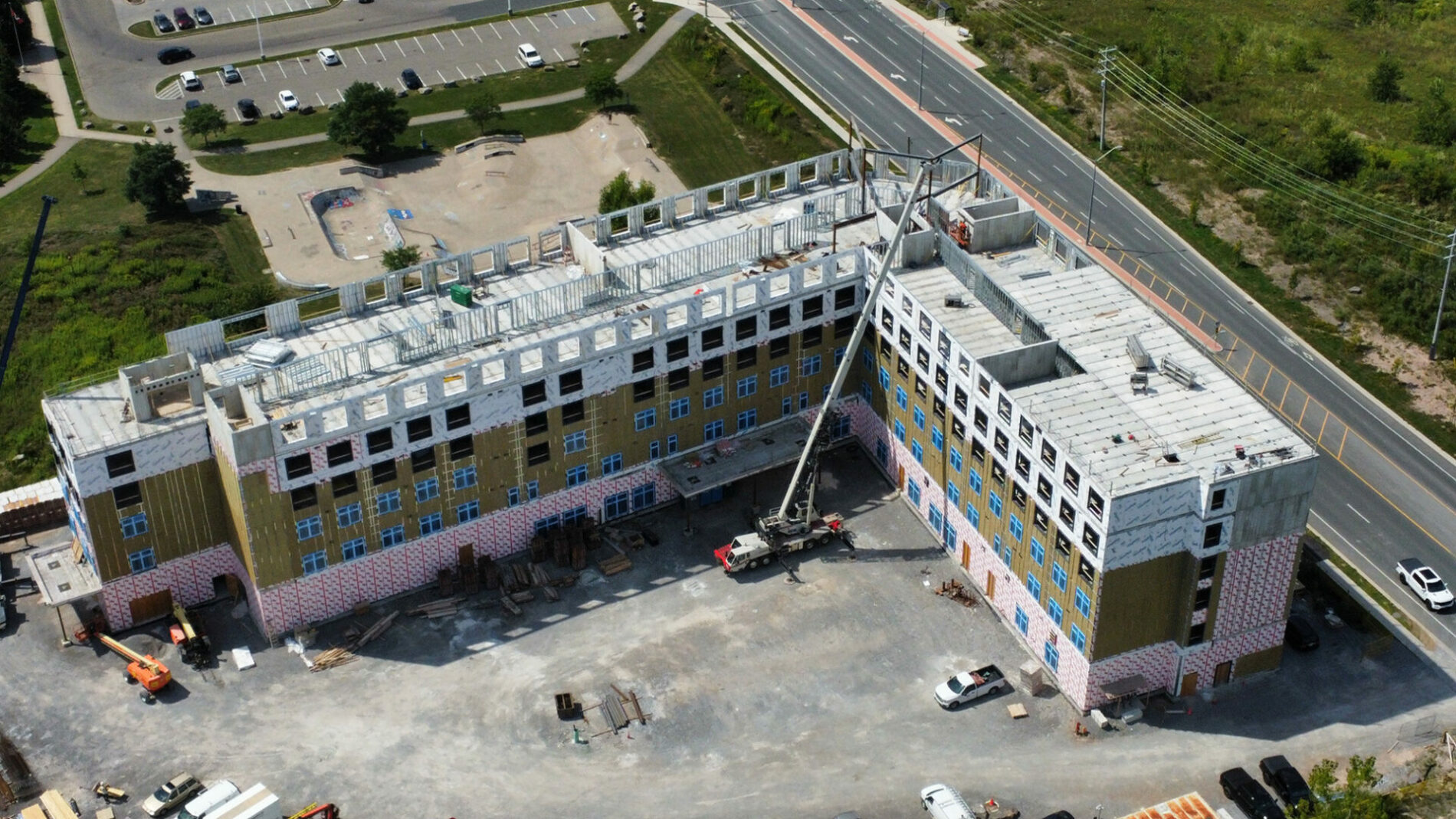
After a few years of working with cold-form steel, Magest found it’s flow and began to expand its offerings. “Magest decided to take responsibility for the structural steel supply and install as well as the floor and roof systems, basically completing the entire upper super structure utilizing our CFS system as much as possible. This method helps to alleviate the general contractors, taking some responsibility off of them with Magest coordinating the superstructure install.” One of the biggest milestones in Magest’s trajectory towards future success was the purchase of a roll former in 2010. “The roll former allowed us to manufacture our own steel studs and track material and fabricate our own cold form steel components, giving us more control over both the cost and fabrication of the wall panels. Our roll former produces stud & track material ranging from 12ga to 26ga studs with 2.5” wide to 14” wide webs. All cold form steel material is produced and fabricated in our mostly automated 95,000 square foot manufacturing facility in Stratford.”
Step by step, Magest evolved from a General Contracting company to more of a one-stop-shop when it comes to cold-form steel, taking on more of the structural design in-house. “When clients come to Magest with a conceptual floor plan, we can help them to design and value engineer their building using our system while keeping cost in mind. Engineering wise, we’ve really jumped into the design of cold form steel. We can provide a complete upper structure design for our clients if they don’t yet have a structural engineer on board. We provide a preliminary structural layout for our clients with a budget price. If that budget price meets their overall project budget, they’ll engage Magest to do the structural design, produce permit drawings, and eventually issue for construction drawings.”
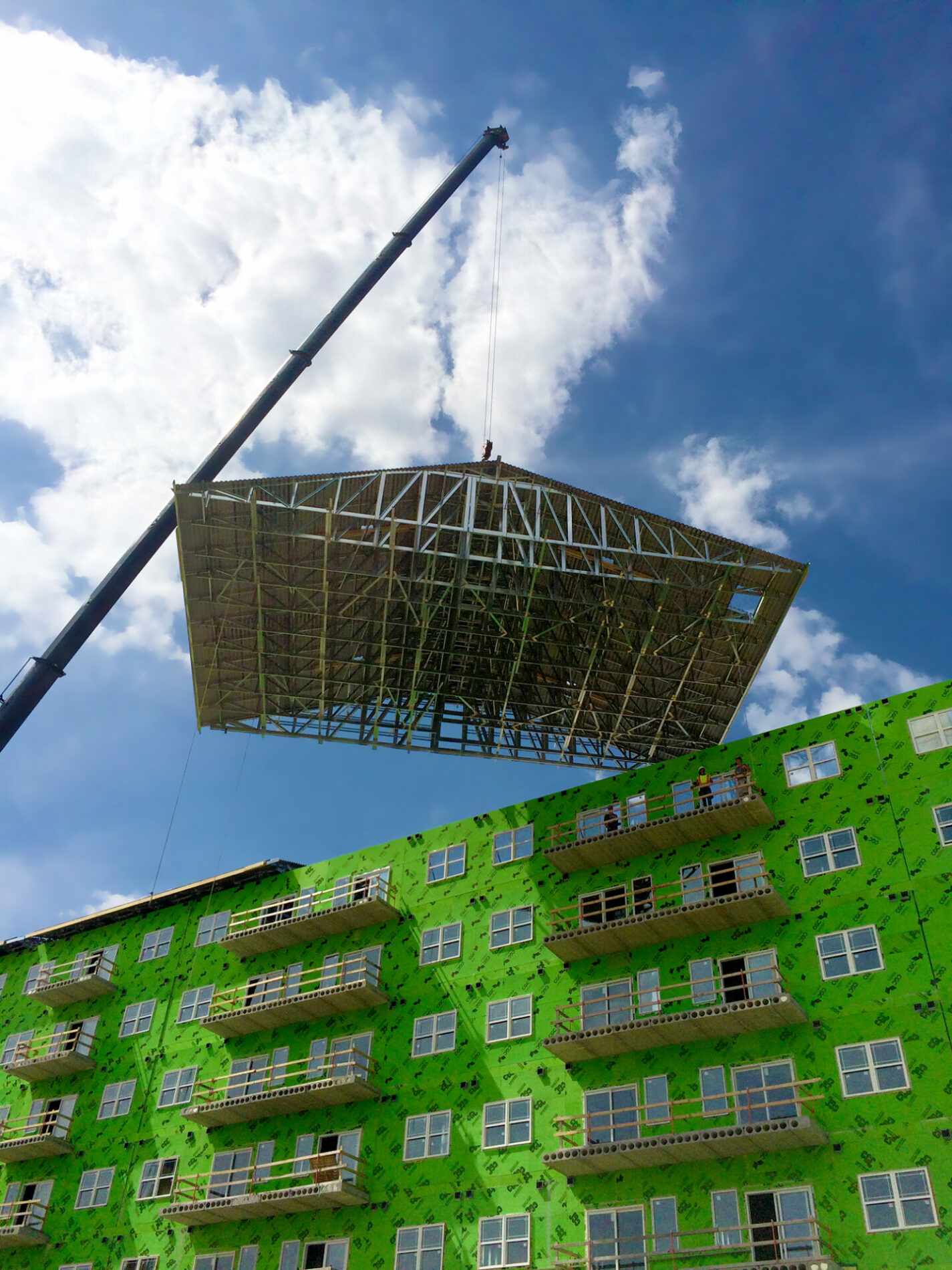
The market quickly caught on to the benefits of Magest’s system, and with this came a larger volume of projects. “We’ve increased the size of our manufacturing facility throughout the years because of the increased demand for fabrication and manufacturing space,” says Craig. “We have seen an increased volume of work year after year as more and more projects are designed in cold-form steel than when we started in 2005. It was difficult in the beginning to persuade architects and engineers to design their projects using load bearing steel stud walls. But now, so many projects are coming out designed in our CFS system, which is great to see. We’re doing something right.” The architects and engineers who once had to be persuaded to design using cold-form steel are now demanding it, and as a result, Magest has experienced consistent growth year after year.
In post-pandemic North America, construction companies have been scratching their heads in search of an answer to the labor shortage that continues to sweep the industry. The old way simply does not work anymore and systems built on efficiency and innovation are carving the way forward. Luckily, Magest was in the game of efficiency and innovation long before the pandemic, and as such can offer a proven, less labor-intensive system that tackles this industry challenge. “With the speed of installation using our cfs system and the skilled trades that we are bringing to site to erect our buildings, there’s less construction labor needed. We try to prefabricate as much of the building as possible, off site. It definitely speeds up the design, erection, and install time, which helps to reduce the overall project schedule. Clients can see how fast our buildings go up, especially if we’re building a six or eight story building across the street from a conventional poured concrete structure. Our buildings are erected in half the time”.
“Now, so many projects are coming out designed in our CFS system, which is great to see.”
Arguably even more important than delivering construction projects within a given program, is delivering them within budget. Magest uses a straight-up approach by which the budget is prioritized from the outset and maintained throughout the process, instead of skirted over and increased as the project progresses. “Being able to maintain the client’s budget along the way is the one of the most important things. The worst thing that we could do is suddenly increase the price at the very end. We don’t do that. If we did, we would never get a call back from that client, and we take a lot of pride in our list of repeat clients. We have so many clients that come to us knowing right from day one that they want to use Magest for their next building. They know what works, and we try hard to keep the cost in check for them.”
As Craig talks me through some of Magest’s projects, the company’s pride in repeat business is evident. First up, the Soleil Condominium development for Mattamy Homes. “Mattamy is a big constructor in the GTA. Approximately three years ago we started the construction of four six-story buildings for Mattamy in Milton.” For these buildings Magest supplied cold formed steel wall panels, as well as structural steel. “The nice part about the Soleil Condos is that all four buildings are on the same site.” This opened up a pipeline of new projects for Mattamy Homes who continue to be one of Magest’s many repeat customers.
Soleil Condos – Mattamy Homes, Milton, ON Varga Condos – Mattamy Homes, Milton, ON
“We’ve also completed ten 4-story apartment buildings for Hyde Construction, who operate throughout Ontario. Each building is 64,800 sq. ft, or 16,200 per level. Magest erected each above grade structure in 8 weeks” Another repeat customer, Magest now do one to two projects a year for Hyde Construction.
“Magest’s construction background has greatly contributed to our success over the years. Knowing how to construct a building on site is just as important as precisely manufacturing the components that go into the building. We understand the details & how the building needs to come together alongside other trades and on schedule. We pride ourselves on the quality of our work and the number of repeat clients that we have.”
As the demand for high-quality retirement services grows throughout North America, Magest has tapped into that market and has completed retirement homes both in Ontario and out of province. “We erected the Rivera Retirement Home in Edmonton, Alberta,” Craig says, speaking of the 4-story 130,000 square foot building in Edmonton that was erected in sixteen weeks. “We have also completed projects in Halifax, North Bay, Sudbury, Niagara Falls and Sarnia. We kind of go all over the place.” Magest’s footprint extends out of country too, with projects in the United States forming part of its portfolio. “We completed a seven-story Harrah’s Hotel and Casino in Murphy, North Carolina, approximately ten years ago.” This project had a floor area of over 160,000 square feet and was erected in just fourteen weeks. Magest’s plan for the future is to continue to respond to market trends while offering innovative building solutions through a system that is proven, efficient, and in demand. With this comes company-wide expansion that will allow Magest to take on a larger volume of projects. “This summer we will be adding a 45,000 square foot plant addition, which will give us more fabrication space. We are also looking into expanding what Magest offers as far as building materials, and that’s part of what the expansion will be used for.”
Of the industry as a whole and Magest’s place within it, Craig sees big opportunity in the increased demand for mid-rise, multi-story residential developments. “I find that multi-story residential is going to grow in smaller communities where they don’t want to expand out with single family homes and encroach on farmland. Smaller communities are now allowing developers to build vertically, to build up as opposed to out. Building 4 Story, 6 Story, 8 Story buildings is exactly what we focus on. I only see our workflow increasing.” With a high-quality system that champions innovation while staying within budget and on program, Magest is all set for a long future in an industry which values those things above all else.