It goes without saying that in the construction industry, waste is not welcome. With rising costs and the drive to create a more circular economy, the concept of materials ending up in landfill is not a palatable one. C&D (construction and demolition) waste includes a vast array of material. Steel, wood products, drywall and plaster, brick and clay tile, asphalt shingles, concrete, and asphalt concrete. These materials are unfortunately end up landfill, deriving from construction projects and sectors such as buildings, roads, and bridges. According to the U.S. Environmental Protection Agency, latest figures show that the C&D sector accounts for an astonishing 600 million tons of debris and waste every year. For an industry that is trying to change public perception and be seen as net positive contributors to the growing climate emergency, statistics such as these aren’t helpful.
However shocking these figures may seem, headline statistics may not be the fairest method of passing judgement on a sector. In fact, if we drill down into the industry, changes are taking place in a variety of forms. Calls for the use of sustainable materials are growing by the day and environmentally friendly methods are gathering speed across the industry. The construction world is, despite the narrative that plays out in some quarters, playing its part.
As with anything however, more can always be done. As we find ourselves in an industry that is no longer happy to accept carbon neutral, carbon negative has now become the goal in terms of generating emissions. So, with that in mind, where does material waste fit into the conversation? Within an industry where deadlines and efficiency are a core feature, it is interesting to note that unlike most other aspects of a successful business, the key may be found by simply slowing down.
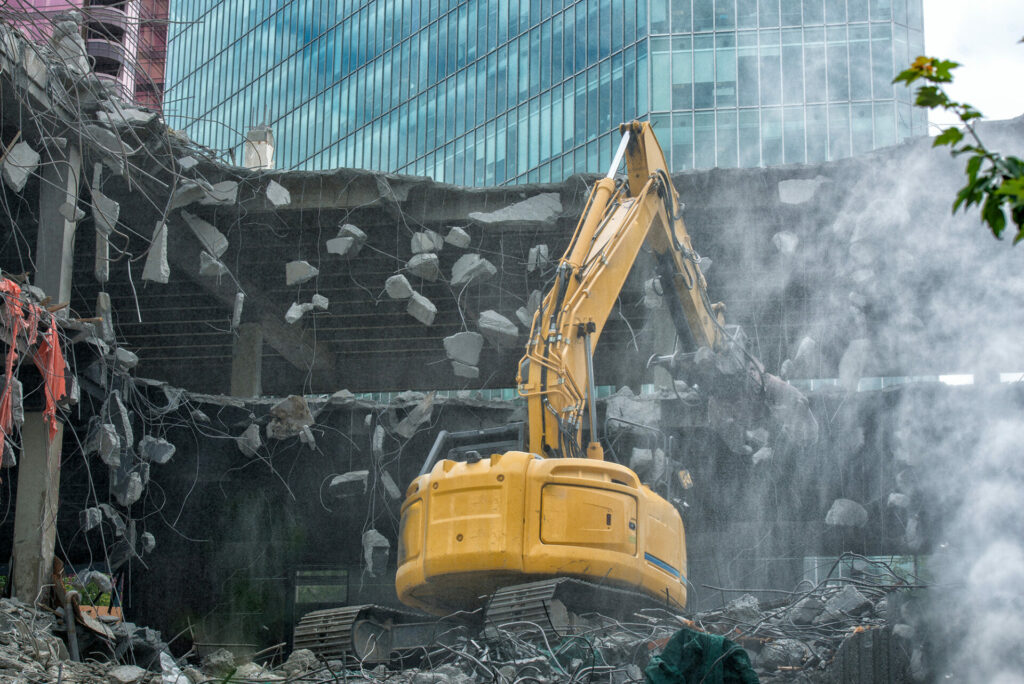
The United States is in the midst of a housing crisis. With widespread acceptance of this and stakeholders from every industry holding opinions on how it should be tackled, the market is not in a good place. However, the incredible truth is that despite this, hundreds of thousands of homes are demolished every year. The reasons for this are a combination of safety, location, and trends. Unfortunately, some homes are no longer fit for purpose. While this may be a bitter pill that we need to swallow, we can look for the potential positives. With these demolition projects racking up the aforementioned 600 million tons of debris each year, some can be salvaged. Unfortunately, by its nature, the process leaves much of these materials unusable. While concrete can indeed be recycled, a significant amount, some 145 million tons, also ends up in landfill. So, in an uneven landscape, where are the positives?
The Birch Group is a Minneapolis non-profit construction company that specializes in the sustainable reuse sector. Having amassed a huge amount of experience across all facets of construction, the company is currently working on growing the number of clients that avail of its Deconstruction service. This process is not merely a token nod to sustainable practices, either. The company identifies savings for each client, explaining that by prioritizing ‘waste diversion’, residential, commercial, and mixed-use renovation projects can yield significant cost savings. “With 27 years of experience in rehabilitating dilapidated residential, commercial, and mixed-use properties, we have an in-depth understanding of the expenses involved in property renovation, remodeling, and redevelopment. Our exceptional expertise in building material reuse makes us unparalleled in waste diversion initiatives.”
“Our purpose is to revive and reinvigorate materials that have reached the end of their useful life, while also fostering a sustainable future for all.”
Deconstruction is a term that can often be mistakenly grouped with Demolition services. While essentially, the result is the same on the ground, the process and benefits are markedly different. In fact, according to the Birch Group, the impact of deconstruction goes much further. “Our purpose is to revive and reinvigorate materials that have reached the end of their useful life, while also fostering a sustainable future for all. Through our work, we aim to revive communities, promote environmental protection, and create job opportunities through workforce development.” By taking a considered and skilled position, each project is approached with care and planning.
Birch Group describes its process in three parts, with deconstruction standing alongside the pre- and post- stages. From site visits and comprehensive inventories to Environmental Impact Reports and grant application documents, everything is covered. It is what happens during the deconstruction process itself that holds the most benefit for clients though. Led by experienced carpenters, the team carefully removes all identified reusable materials. At the helm is deconstruction expert, Petrina Rhines.
Having completed a carpentry apprenticeship three years ago, Rhines decided to pursue a more innovative approach to the reimagining of the city’s decaying buildings. By picking apart each building, removing materials in a manner that leaves them in reusable condition, the projects are disassembled, rather than flattened. In addition to that, the materials are then sold by the Scrapbox Salvage store, a non-profit salvage company that aims to “reclaim and harvest everything from lights, flooring, windows, doors and more for resell to the public.” With a new inventory arriving in store each week and assistance with accessing tax savings and installation grants, the store is proving to be a huge hit. This partnership stems from a shared view of how materials should be treated. Instead of bulldozing, we should slow down a little and look at what we are doing. According to Rhines, the reason for setting up Birch Group is a simple yet vital one. “Essentially, we’re trying to keep as much trash out of the waste stream as possible. We’re doing all of this by hand too, so we’re also reducing a lot of pollutants that would go into the air.”
While deconstruction by hand certainly has its benefits in terms of salvageable materials and environmental practices, it may not be the most effective tool to combat 600 million tons of waste. Thankfully, that is where education comes in. With a staff of 25 and growing, Birch Group is certainly seeing its message spread locally. By sharing information about the process even further, the hope is that it may catch on to become something remarkable. Birch Group has struck up a partnership with Hennepin County and Reuse Minnesota, a professional network to advance the reuse sector, offering workshops and presentations to a number of local high-schools. By reaching the community at a younger age, Rhines is hopeful that things will change over time.
Only one year in, Rhines and Birch Group are changing the narrative. While it may still be early days, it seems that deconstruction and the benefits that come from it could potentially be life-changing in more ways than one. “The training for deconstruction careers is short. You can learn on the job and get started in a career in a short period of time. College isn’t for everyone, and we are just showing students that there are other opportunities out there. More than anything though, we’re trying to catch them while they’re young and instill in them sustainable business practices. Hopefully they will carry that sustainability mindset through their lifetime, and they will become lifelong learners within the sustainability world.”