In a post-pandemic world, it seems as though challenges are mounting. The cost of living is rising to extreme levels while concerns continue to grow around environmental and social issues. Underpinning this sense of anxiety is the acute shortage of residential housing, a problem that seems to be facing every community worldwide. The construction sector is, unsurprisingly, at the center of these challenges. It is an industry that is seen by some as both the cause of these issues and its potential savior. With innovative new techniques, materials and designs coming onstream every day, it seems that much is being done to work through a challenging environment. However, in recent times, one particular development has offered a glimpse into a future that is both equitable and sustainable. In order to meet the growing demand for affordable and sustainable housing, innovative companies have turned to 3D printing. This exciting development, offering a cost-effective and eco-friendly solution to the housing crisis, benefits from minimal waste, quicker build times and a lower carbon footprint.
While 3D printing has certainly made those in the construction world sit up and take notice, it hasn’t yet taken over. Techniques are advancing and appear to be close to a level that could be rolled out on a wider scale, but a number of factors leave it at risk of stagnating. Prohibitive costs and a lack of knowledge across the industry are evident barriers to its ongoing success. However, for a sector that thrives on novel and innovative advancements, it shouldn’t be that way. The potential benefits of 3D printing in relation to the construction industry could not be clearer. It is incredibly fast, for starters. Amidst a housing crisis, this is reason alone for the sector to be prioritized. Despite these benefits, it is an area still in its infancy. Start-ups are appearing in small numbers and highly impressive mini-projects are breaking ground but thankfully, that may not be the case for very long.
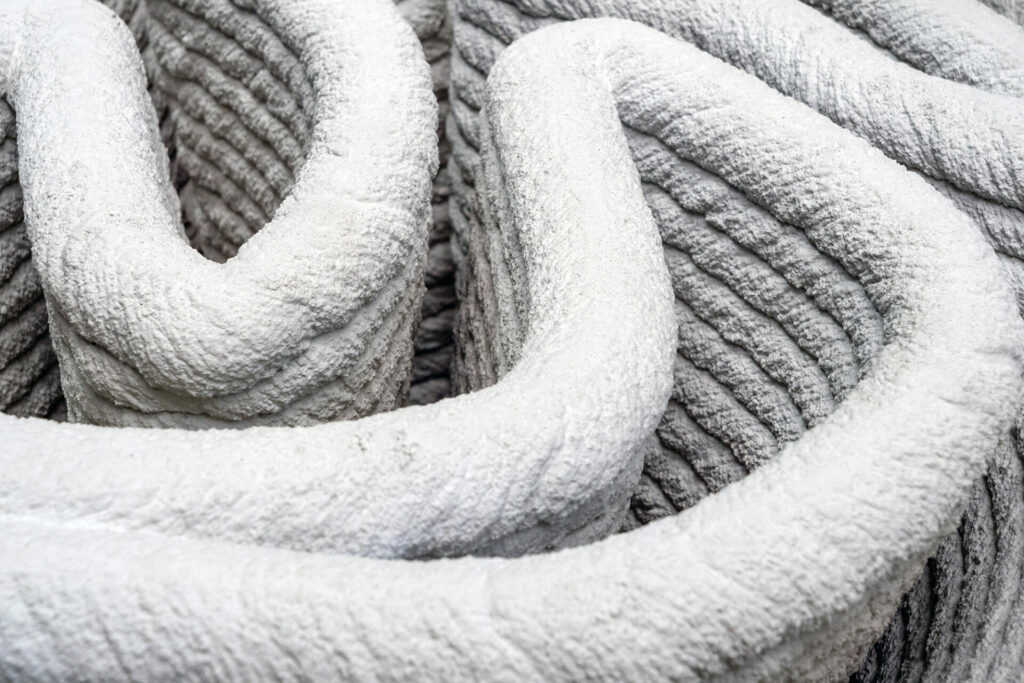
The culmination of a two-year collaborative effort between architectural designers Leslie Lok and Sasa Zivkovic, principals of HANNAH; along with PERI 3D Construction, and CIVE, one of the leading engineering and design/build contractors in Houston has resulted in the ‘House of Cores,’ the first ever two-story house built by using a 3D printer. The structure, an incredible 4,000 sq ft, is designed and produced to showcase the vast potential that 3D printing can potentially have on the housing market. According to HANNAH, the house has, unlike other 3D-printed structures to-date, a customized design and has been built through design solutions that weave existing construction methods with new technology. “With a hybridized construction method that combines concrete 3D printing with wood framing, this approach allows the two material systems to be used strategically and aims to increase the applicability of 3D printing in the U.S., where framing is the one of the most common construction techniques. The building design is conceptualized as a series of printed cores that contain functional spaces and stairs. The spatial cores are connected by wood framing to produce an architectural alternation of concrete and framed interiors. The project’s scalable design and construction process is applicable for multifamily housing and mixed-use construction.”
The printer, the COBOD BOD2 gantry printer is an enormous piece of equipment that weighs more than 12 tons itself and is the work of cutting-edge 3D construction company, PERI. By utilizing the printer’s ability to work through custom designs and effective layout capabilities, the structure a three-bedroom house, was erected in an incredible 330 hours. According to Fabian Meyre-Broetz, CEO of PERI, the project demonstrates the company’s ability to lead the way when it comes to modern construction methods. “We are incredibly proud to not only showcase the possibilities of the BOD2 3D construction printer but also our extensive know-how in planning, engineering, and printing on this project, which is the seventh and largest one we printed so far. We are convinced that it will set new standards from a design as well as printing execution perspective and underlines our role as the forerunner for this new construction technique.” This view is echoed by Lok who believe that, due to the intrinsic challenges when building a two-story building, the printer itself was a vital aspect of the project’s success. “You can actually find a lot of 3D-printed buildings in many states,” Lok said. “One of the things about printing a second story is the technical requirement of the machine. And of course, there are other challenges: structural challenges, logistic challenges when we print a second-story building.”
“By consolidating traditional methods and harnessing the potential and power of cutting-edge techniques, the construction industry has once again come up with a solution that may yet revolutionize the housing sector.”
While the project is the culmination of work from many parties, the work on the ground is being completed by CIVE, the Design-Build firm that looked after the engineering and GC work. In a sector where sustainability needs to meet with functionality, the project could be a crucial turning point in the challenging environment facing both the construction industry and the housing market in general. For Hachem Domloj, President at CIVE, it marks an enormous turning point. “Having the opportunity to be the engineers and general contractor for the first multistory 3D-printed structure in the U.S. has been an honor. We can see how this technology and our team’s approach is providing the scalability to larger commercial developments. Collectively, we’re changing the way our country builds, and paving the way for more affordable housing, higher structural integrity, and faster building capabilities. The possibilities of 3D printing are endless!”
Photo credit: HANNAH Photo credit: Anthony Vu
With the need for more housing growing, it seems as though time is not on anyone’s side. Supply chain issues, skilled labor shortages and rising costs are all compounding a situation where a solution needs to be reached immediately. However, the ‘House of Cores’ is a genuine breakthrough. On this project, 3D printing has moved from niche to mainstream. It is no exaggeration to suggest that this could signal the beginning of an end to the crisis. As for those involved, the structure is already a massive success. By consolidating traditional methods and harnessing the potential and power of cutting-edge techniques, the construction industry has once again come up with a solution that may yet revolutionize the housing sector. “For the design of the project, we developed a hybrid construction approach that couples innovations in concrete 3D printing with traditional wood framing techniques to create a building system that is structurally efficient, easily replicable, and materially responsive,” said Leslie Lok and Sasa Zivkovic, of HANNAH. “The project also highlights the exciting design potential of mass-customized architectural components to meet homeowner’s needs and to simplify building system integration. These design efforts aim to increase the impact, applicability, sustainability, and cost efficiency of 3D printing for future residential and multi-family buildings in the U.S.”